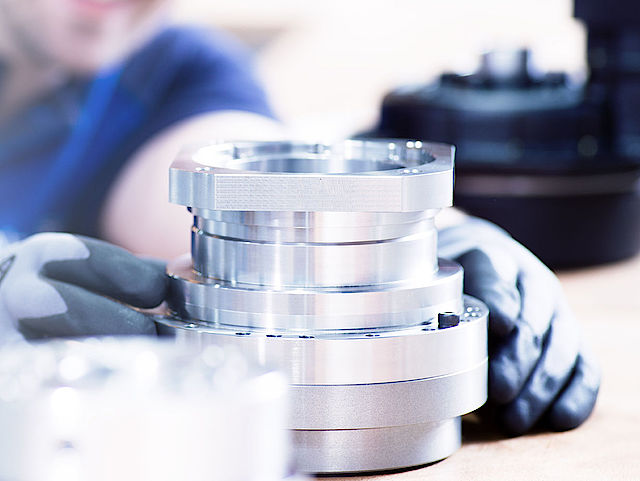
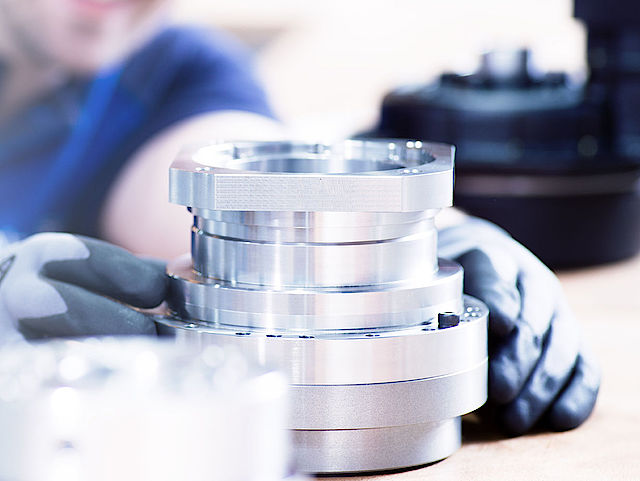
Read more of the latest news from Nabtesco. Discover our company news, specialist articles, press releases and LinkedIn Posts.
Issues such as sustainability, energy efficiency, Industry 4.0, automation, robotics, individualisation, digitalisation, and artificial intelligence (AI) are currently some of the strongest drivers of innovation in drive technology. These megatrends are defining technological progress in the field of drive technology as well. How will Nabtesco meet the challenges, and what will be the special focus in 2024? Daniel Obladen, Head of Sales General Industries at Nabtesco Precision Europe GmbH, explains.
How will the trends mentioned above continue in 2024? What developments are to be expected in drive technology?
Daniel Obladen: The impulses come primarily from the areas of software and control electronics. Industrial Internet of Things (IIoT), embedded systems, big data technologies, artificial intelligence, machine learning, low-code/no-code concepts, cloud services, edge computing, etc. – all of these trends will have a lasting effect on drive technology, this is where the major leaps in development can be expected. But software is only one side of the coin. The other side is hardware. The performance and efficiency potentials of software can be fully exploited only in combination with advanced hardware technology. One can make a comparison to the world of sports. Top athletes need the right equipment. The choice of running shoes can decide victory or defeat. It’s the same with drive technology. Still, we often see companies investing heavily in modern software, while the hardware, including the gears, tend to be neglected.
What does that involve in concrete terms? What role do gears play in achieving more efficiency, safety and functionality in drive technology?
Daniel Obladen: For converting torque and speed, gears are a central element in the drive train of machines and systems, where they have a major effect on performance and efficiency. They define the production cycle, so to speak. That is why special care is needed when choosing and designing the gear unit. Let’s have a look at safety, for example, which is currently a major issue under discussion in automation and robotics, as well as medical technology. The majority of users focus almost exclusively on aspects such as sensors, controllers, etc. But what good are the best sensors if the gears or the mechanical drive technology does not fulfil the stringent requirements of the application? Technologies such as our cycloidal gears make the difference here. Their special design makes them particularly resistant to impacts and overloads (shock resistance up to 500% of the rated torque), which ensures a sufficient safety margin for reliable operation. Especially in applications with high reduction ratios, their power density is superior to that of worm gears, for example.
Sustainability is still one of the most important trends in drive technology. What are the advantages of cycloidal gears?
Daniel Obladen: Since they are designed to be highly resistant, cycloidal gears have an above-average service life. High-quality, long-lasting products save resources and make a significant contribution to sustainability in drive technology. A good indicator for the life of gears is their overload capacity. For cycloidal gears, this capacity is two to three times higher than that of planetary gears. The decisive factor here is the transmission of power by cams and rollers. This design ensures virtually full contact and even distribution of forces within the cycloidal gear unit, which produces high rigidity. In addition, highly integrated angular ball bearings, which optimally absorb both axial and radial loads, ensure a high load-bearing capacity. Compared to conventional technologies such as planetary gears and worm gears, cycloidal gears are also designed for minimal wear. The increase in backlash is extremely low, even over long periods (max. hysteresis loss 0.5 to 1 arcmin).
Which direction will energy efficiency take?
Daniel Obladen: Energy efficiency is currently the number 1 megatrend in drive technology. This will not change in 2024, in view of rising energy prices and ever more stringent regulations. Hybridisation, electrification, and downsizing are the concepts of the future. For example, heavy loads are often still moved using hydraulic systems. Such systems are bulky and inefficient. Cycloidal gears guarantee precise positioning even in the case of heavy loads, which makes them an efficient electromechanical alternative, for example for moving large panes of glass, metal sheets, machine components or even entire vehicles. Thanks to their rigidity and compact design, they also allow the construction of smaller machines and systems. That has a positive effect on the consumption of power and resources, as well as overall operating expenses.
What is actually meant by hybridisation?
Daniel Obladen: Hybridisation means the combination of different technologies, for example combining mechanical components, such as our gears, with supplementary digital services. This creates genuine added value for the customer. Hybrid concepts such as digital gear twins create performance and efficiency advantages in drive technology. For example, a Nabtesco robot control add-on can increase robot precision by a factor of 9. In the future, high-precision handling and processing tasks can be carried out by a robot with the precision of a machine tool. The digital gear twin will also play a central role in real-time monitoring of robots, since it allows an individual snapshot of the robot utilisation and therefore analysis of the remaining life of each single gear in the robot. The trend is toward virtual sensors.
What are the current trends in the field of drive technology?
Daniel Obladen: Automation, digitisation, Industry 4.0, availability and mass customisation will still be relevant in 2024 and beyond. Other trends include concepts such as low-cost robotics and simplicity. Low-cost robots are inexpensive and user-friendly, thus making it easy to get started in the world of automation. They are especially suitable for simple handling tasks with low requirements for precision and dynamics. Simplicity is about reducing complexity, which reduces both susceptibility to faults and costs. The Neco® series is an excellent example of this approach. By focusing on perfection, we created a very economical solution without having to make any compromises regarding the technical specifications.
What do you consider to be the causes for increasing automation?
Daniel Obladen: Driving factors include the shortage of skilled labour, reshoring (bringing production capacities back home) and cost reduction. Higher efficiency, higher productivity, reduction of the employee workload and better efficiency are key issues here. Technological progress also plays a role. Meanwhile, there are robotic solutions for cleaning sausage cases or for bin picking of unsorted objects. Until recently, this was not possible with existing technology. Automation of processes in such applications required the development of optical systems that can process data in real time.
Important drive technology trends in 2024:
Would you like to learn more about drive technology trends in 2024, our high-performance gears, or our innovative solutions for robotics and mechanical engineering? Then don’t hesitate to contact our experts.